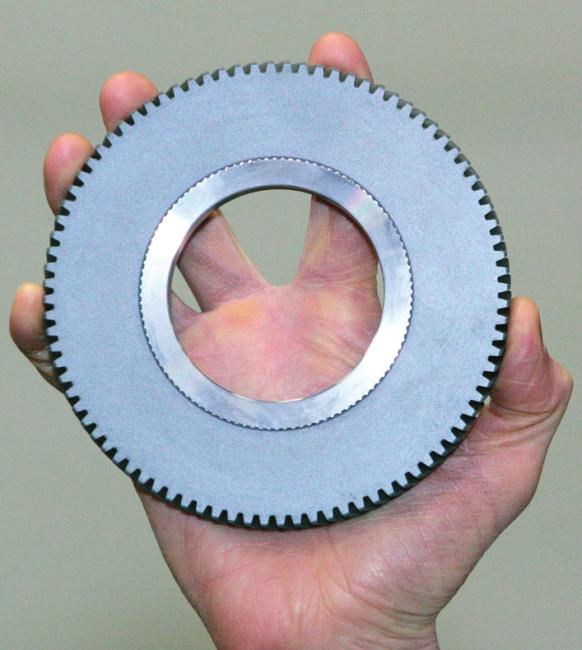
Edgerton gearmaker finds niche in nylon-steel products
“I just want to say one word to you. Just one word. Are you listening? Plastics.”
—Charles Webb’s novel “The Graduate”
EDGERTON
Picture giant machinery in any factory, anywhere. Images come to mind of networks of machines powered by heavy metal gears, each machine’s moving parts constantly being oiled and lubricated with hoses and pumps.
Another part of that picture: A dirty machine engine, changed out by workers, drips and spatters on the concrete floor. Somebody’s got to clean that up. Then, maybe, something goes wrong with a big, important gear. Metal rasps on metal, and things grind to a halt.
Local gear manufacturer Edgerton Gear has made it part of its business to help industries avoid almost all of that. It’s about plastic. And metal. Both fused together. And it’s changing the way a lot of companies are able to do business.
Over the last 15 years, Edgerton Gear has developed a specialty line of gears, rollers and sprockets under the name Duragear and a patented system to build the components. The gears are made of special nylon—four different types, with various strengths and properties— which is fused onto a metal core through a process that’s proprietary. It involves magnetic force and heat, and that’s about all Edgerton Gear owner Dave Hataj will say.
The gears were developed by a partnership between Edgerton Gear and Quadrant, a plastics company that manufactures the ultra-strong nylon used in the gears. Edgerton Gear fuses the nylon to metal cores in-house and cuts worm-gear teeth into gears and sprockets based on specifications for individual companies that use the products.
Duragear serves a growing niche for manufacturers who seek—or need—to run cleaner, with lower maintenance costs. The secret: When you mesh metal gears with nylon gears, there is less friction, dramatically lowering risk for major gear failure and no need for machine oil to lubricate gears.
The oiling issue also is important for some companies, particularly those in the growing food processing and packaging sector that must adhere to strict USDA food-handling guidelines. Take, for instance, one New Jersey company for which Edgerton gear supplies food-grade nylon-steel rollers and other components:
“All they do is their machines take hamburger and make it into patties,” Hataj said.
Alkar-J-Conn, another company that processes hot dogs, uses Duragear parts to trundle long links of hotdogs that hang like meat curtains from huge, hanging conveyor systems.
You can’t have a lot of oiled machine components around burgers and dogs.
Edgerton
Gear, which is at 20 Gear Drive, Edgerton, is one of the only companies
in the U.S. that produces the fused plastic-metal gears. It’s a side
division of the company, which also produces traditional metal gears for
companies as diverse as print plants to powered construction equipment.
There’s
a growing need for gears that don’t require oil and can hold up under
intense production processes, Hataj said, and one the company has just
started to tap, even after 15 years. Edgerton Gear doesn’t run a major
advertising push for the product, Hataj said. Customers find Duragear
with just a cursory Google search because, well, they’re about the only
company in the U.S. that makes such parts.
“We’ve
been doing this for a while, but it’s such a specialized product that
it’s a challenge to find the right markets. It just now getting growing
potential. More and more specialized manufacturers are looking for cleaner solutions and gears that hold up in aggressive environments.”
The
company is one of a few that have formed a partnership with Edgerton
High School to offer paid apprenticeship programs to high school
students. The students work at the gear shop, alongside seasoned shop
pros, learning the ropes. The hope, Edgerton Gear owner Dave Hataj has
said, is that he can groom a young work force that wants to stick around
to move Edgerton Gear forward as more and more manufacturers begin to
innovate.
Here’s what Hataj
means by “aggressive environments”: Stolle Machinery in Denver, Colo.,
one of Edgerton Gear’s major customers, makes can “pucks,” the tops and
bottoms of soda and beer cans used by 95 percent of beverage companies
on every continent in the world.
Stolle’s machines stamp out “pucks” at a ridiculous rate: 3,000 a minute, 365 days a year.
“When
you watch those machines go, you can’t even see the parts going. That’s
how fast they move,” Hataj said. Still photographs only pick up a blur.
The
company began using Duragear parts because their heat-treated
nylon-steel construction holds up under the incredible stress, heat and
wear-and-tear of the can-stamping machines’ relentless and punishing
pace.
Huge commercial
printing facilities have machines with main gears that are
affectionately, or not quite so affectionately, known as “blowout
gears.” Those gears take the brunt of stress in production. An advantage
Duragear and its customers have seen is that nylon-steel “blowout
gears” hold out better, and if they do warp or fail, they’re faster and
easier to swap out with less downtime.
“They’re just cheaper and easier to replace,” Hataj said.
Hataj
has a business model that few locally even know about. He’s even a
little hesitant to disclose the details. It’s as innovative as his line
of nylon and steel gears.
The
Duragear line, he said, runs essentially as a nonprofit. That is, most
of the proceeds from the sale of Duragear products fuel various
philanthropic causes that Edgerton Gear is involved in. The company has
used Duragear proceeds to donate to different programs and causes in
Honduras.
It’s just
one part of ongoing programs that Edgerton Gear is involved in at its
own cost. Locally, the company is one of a few that have formed a
partnership with Edgerton High School to offer paid apprenticeship
programs to high school students.
The
students work at the gear shop, alongside seasoned shop pros, learning
the ropes. The hope, Hataj has said, is that he can groom a young work
force that wants to stick around to move Edgerton Gear forward as more
and more manufacturers begin to innovate.
“You
can say, yeah, OK. You make gears. But the thing is, gears make
everything you see. Who hasn’t drank a soda from a can made from
‘pucks’? Innovation is everywhere.” Hataj said. “Here, we’re just lucky
to have a window into it and to be involved in a part of it.”